We change – So you don’t have to!
6 April 2022
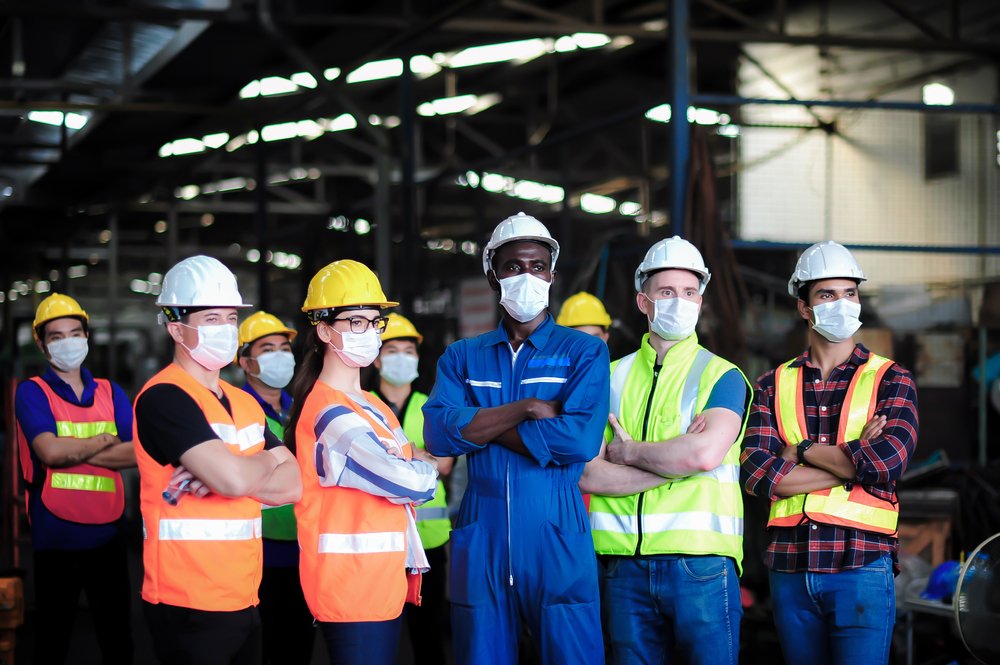
Leverage what you already have invested in – your people, programs, and procedures
Let us start with a premise that most facilities, through company policies and industry guidelines, laws, and regulations, have built site-specific programs, practices, and procedures to support their daily operations and safety processes. To be clear, the conversation is not about how documentation is stored, how training is implemented, or the need to modify programs, practices, and procedures in place but rather what can be done to enhance existing processes through the use of electronic desktops and mobile integrated solutions. We understand that you are probably doing things well-beyond industry standards and guidelines. If you were not, you most likely wouldn’t be in business anymore and wouldn’t be reading this article. If you agree with the point above, in all likelihood you may be one of the many companies looking for software solutions that add value to how you perform and execute these critical tasks and activities.
Most companies have devoted decades to building, documenting, and training on programs, practices, and procedures required to provide a safe work environment that meet the regulatory compliance within their industries. Many of them are very proud of their incident/accident rate, lost-time injury frequency, and overall culture of health, safety, and environmental responsibility, and they should be! Over the last decades, Companies have invested millions in industry consultants and staff expertise to help in critical areas such as Mechanical Integrity, Environmental, Health and Safety, Risk Mitigation, Engineering, and Production to install programs related to environmental, occupational, and industrial safety, risk assessment, hazard analysis and equipment reliability. Methods such as root cause analysis, various investigation technics, and audit/review driven by continuous improvement and optimization approaches have been used to enhance efficiency, productivity, compliance, and safety.
So why change these processes?
The answer is you shouldn’t have to and don’t have to as there are solutions that can digitize and enhance what you have now. The gap to be addressed is how digitalization of the existing processes such as site-specific audits, inspections, checklists, Shift Logs, isolations, and permit-to-work, including the systematic procedure of tracking and managing the execution of said processes can best be achieved. Through optimization and continuous improvement efforts, in addition to departmental challenges to increase daily work activity efficiencies, software and mobile solutions are becoming more prevalent within the “day in the life” of operators and maintenance technicians. Through the use of handheld devices, ruggedized tablets, laptops, printers, and barcode scanners connected to cellular or Wi-Fi networks, plant personnel can now more efficiently and safely track, manage and execute critical tasks and activities in their complex, large, and spread out facilities. The way this critical information is collected, tracked, managed, and shared within a facility significantly affects daily production, environmental impact, and the safety of people and the community in either a positive or negative way.
Let us take a look at the process of migrating from paper-based systems developed over decades, to electronic software solutions which provide additional capabilities and use of mobile technology. Even though there have been significant advancements in production & maintenance management, supply chain, HR, and all the other facets required to manage multi-site and multi-million, if not billion-dollar companies, have you done enough in the area of operational processes digitization? Especially in areas such as lockout/tagout, logbooks, operator rounds, safety checklists, inspections, environmental audits, or control of work, all of which are critical processes.
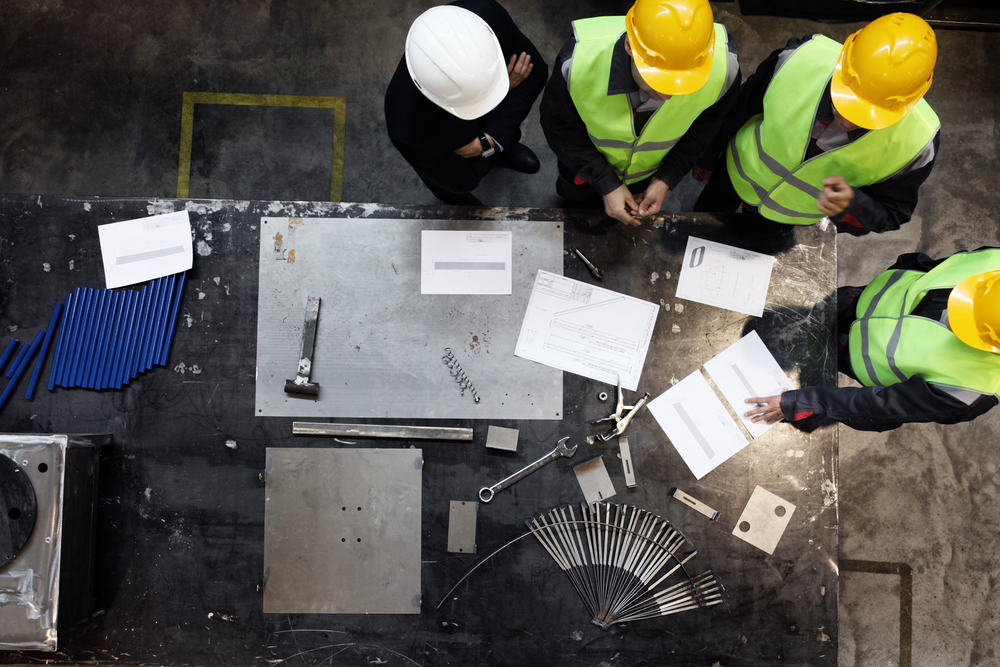
Companies that operate in high-risk environments or facilities using complex infrastructures and procedures with hazardous materials which include corrosive, toxic & explosive components should ask the question of how much of the actual daily tasks and activities have been electronically optimized and what tasks are still performed with paper that is more difficult to track and manage efficiently.
When considering the change from paper to electronic systems important questions to ask are:
- How well are your existing solutions, electronic or manual, integrated,
- how are communication and broadcasting of information performed between engineering, operations, maintenance, environmental, and safety departments,
- Will new mobile technologies provide optimization of the current paper process while improving safety and compliance?
- Where do paper processes cause inefficiencies or potential error (i.e. collecting data on paper and having to decipher handwriting to enter it back into a system when returning to the control room or office)
Departments or groups searching for and trying to implement targeted tools to address a perceived need or pain point or wanting to streamline the activities while striving for optimization through automation & technology are often struggling to find the right solution. The right solution is one that causes minimum disruption to their business and that could fit in the company’s overall strategy and procedures while maintaining an easy to manage information flow between departments. Many have tried various approaches often using off-the-shelf single-point solutions. An example would be an Operator Round system used for capturing additional production data not available through an existing Distributed Control System (DCS) or Supervisory Control And Data Acquisition (SCADA) system. Not having such a system integrated with other modules such as a Data Historian, an electronic Logbook, or even a Permit To Work could limit the efficiency and productivity of the facility by creating duplication and preventing access to critical information. Sending that data automatically to an existing Data Historian or a logbook provides a better real-time view of the plant condition and health.
Changes in our Industry
The pandemic has accelerated and even in some cases initiated dialog on how to move towards better digitalization of operational processes. Today’s workforce is eager to embrace new technology such as mobility to optimize what would be traditionally a paper process and reduce the amount of shared contact with such paper documents. Ruggedized mobile devices and intrinsically safe devices are now available that have allowed the use of such applications in the workplace rather than just using mobile devices in our social and home lives. However with innovation comes new challenges such as integration, platform incompatibility, infrastructure expansion, and of course cybersecurity not only for the people implementing the solution but also for the user population in terms of learning new processes and adapting to new forms and screens. Finding a well-integrated mobile electronic system that can model multiple processes such as LOTO, Permit to Work, Risk Analysis, Management of Change, Incident Tracking, Logbook, Round and Inspections, and Checklists and still closely replicate your site-specific processes and forms, is the goal of the majority of safety managers.
Want to explore further?
We do understand that change is hard and needs to be minimized especially when it affects efficiency, productivity, compliance, and safety.
If you are interested in learning more about such a Suite and would like to take the next step in digitalizing your existing Process Safety Management and Environmental, Health programs and procedures, get in contact as this is an area that we have experience and would love to discuss how we can build your own “Operations Management Solution”.
To learn more about our proven eclipseSUITE of Operational Management Modules and how our professional implementation can improve your Operations and Safety Management, please contact us at sales@nisoft.com or visit www.nisoft.com for more information.
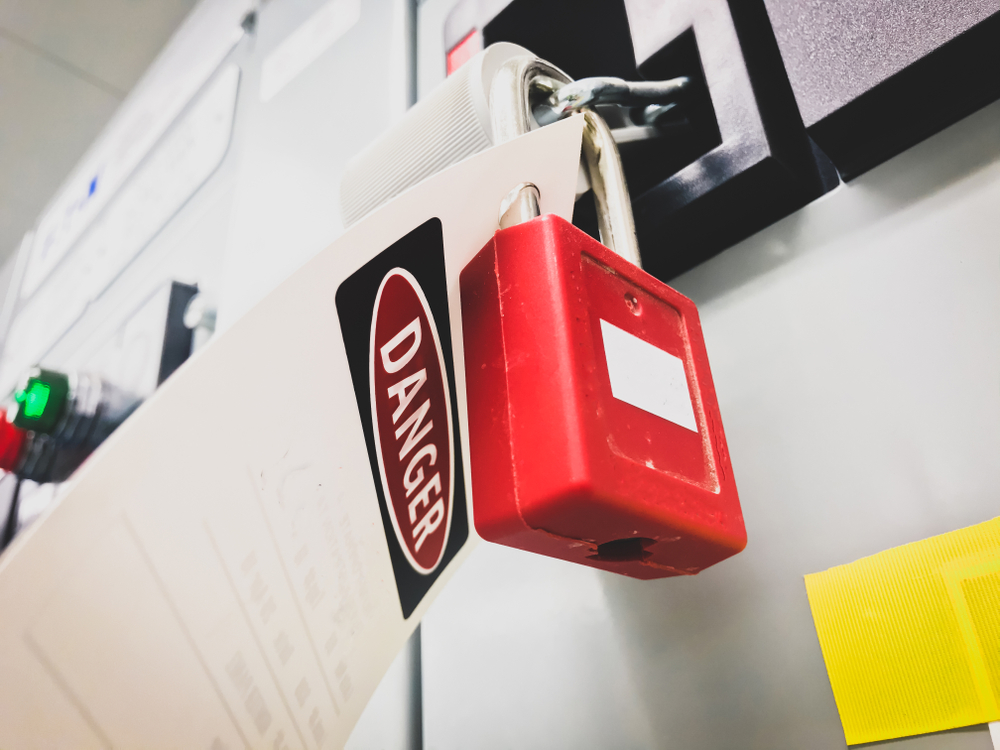